DC Position Control System , Model : DCP – 132
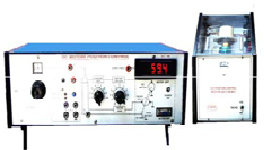
Features and Specifications
- Compact system - no mechanical hassles Simplified operation
- Digital storage of transient response (step mode)
- Positive/Negative tacho generator feedback
- Position control of a 12 volt, 1 Amp dc geared PM motor ( 50 / 60 RPM )
- Calibrated dials with 10 resolution for reference and output position
- Two 3600 servo - potentiometers
- Built in step signal
- Inbuilt tacho generator with polarity reverse switch
- Calibrated forward path gain 3 to 10 in steps
- Calibrated tacho constant 0.2 to 1 in steps
- The motor unit is housed in a separate cabinet with transparent Cover for easy viewing.
- Interconnection with the main unit is through a standard 9-pin D-type connector. All power supplies and step input signal are internally provided. In addition a 3½ digit DVM is available on the panel for the measurement of various signals. A good quality measuring CRO is the only accessory that would be required.
- Built in waveform capture / display card for study dynamics in step mode
- IC regulated dc power supplies for circuitry
- Dimension : 410x215x140mm main unit approx)
- Weight : 3.5 kg main unit (approx.)
: 215x160x130mm motor unit (approx.)
: 2 kg motor unit (approx.)
List of Experiments
- Operation of the position control system for different values of the forward gain to angular position commands(effect of forward path gain in steady state error)
- Step response studies for various values of forward gain(to analyse the transient)
- Study of the effect of velocity feedback on the transient and steady state performance of the system as well as its stability(Effect of velocity feedback upon transient response)
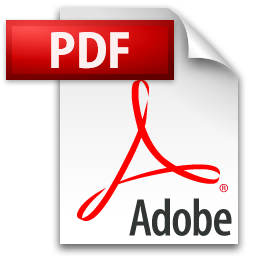